利用合作科研设计和优化电芯案例探究
利用合作科研设计和优化电芯
当前我国致力于减少二氧化碳的排放,将2050年实现净零排放作为目标,因此电池将成为达成这一切的关键。电池制造商、细分领域专用电芯设计厂商、汽车OEM厂商、电动垂直起降(eVTOL)飞机制造商以及电池材料供应商都投入了大量的资源,寻求电池技术的开拓性创新。电池是一个复杂的材料系统,电池的开发需要具备娴熟的专业技能和先进的数字解决方案。
在超过25年的时间里,达索系统的合作科研团队一直都在为汽车、航空航天、高科技、采矿、能源、先进材料、包装消费品、工业设备、医疗卫生、医疗设备等行业的研发领域提供鼎力支持。合作科研团队的专家来自多个专业学科领域,他们凭借3D化学软件工具(主要有Materials Studio COSMOtherm和Pipeline Pilot),形成先进技术能力(ATC)。专有的ATC包括经广泛验证的算法、内容、模型、方法和工作流程。
在电芯设计、组件优化、制造流程改进和人工智能/机器学习驱动下的电池性能预测方面,合作科研团队为客户提供了灵活的协作模式。合作科研团队与工业客户密切合作,对流程、特性和产品提出重大的全新业务见解。合作科研团队帮助客户提升研发能力,加快创新步伐,主动组正缺陷,赋能客户掌握信息进行决策,加快其创新产品的上市。合作科研团队严守机密IP,促成IP的共同受益,按时完成目的明确的阶段性目标,为成功合作奠定完善的基础,推动开发更轻便、优质、便宜、安全和更易循环利用的新一代电池。
合作科研团队已助力向各行业提供电池解决方案。鉴干协作模式的性质,客户案例中只披露高层级信息。
案例一:一家跨国汽车制造商聚焦迈向成功的实验
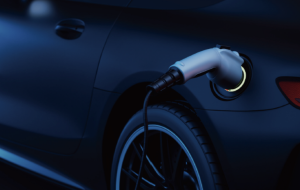
业务挑战
开发新一代电芯需要探索广阔的化学空间,寻找潜在的备选电解液方案,相关实验不仅极为耗时而且成本非常高昂。
解决方案
合作科研团队依托自身的专业能力,为不同的电解液配方体系构建经验证的性质预测模型。仿真采用定制化的专用工作流程。合作科研团队随后模拟电池的运行机理,分析其输运、热以及电化学行为。使用”模型优先”方法,快速筛选不同的化学体系。此外,经验证的工作流程也同样交付给客户,以便于日后进一步使用。
应用成果
- 根据可用的实验数据,验证基于3D化学的物理模型
- 通过电解液虚拟孪生模型来探索海量潜在配方
- 采用基于第一性原理的3D化学方法模拟关键性质
- 通过对于热特性进行虚拟筛选,将安全要素纳入考量范围
- 利用模拟快速甄别备选电解液方案,减少不必要的实验测试量
“根据合作科研专家提供的建模与仿真结果,我们沿着生产力最佳的路径设计并更好地聚焦我们的实验,从而节省30%以上的研发时间”
— 汽车制造商研发总监
案例二:一家跨国汽车制造商定制化工作流加速创新
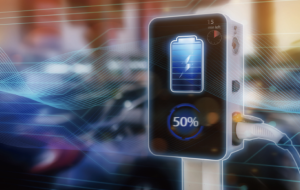
业务挑战
获取工程模型所需的实验数据有时是极为耗时或难以测量的。如电芯的膨胀、内部的枝晶生长、劣化和老化等局部现象的实验数据通常难以获取。
解决方案
合作科研团队运用基于第一性原理的3D化学进行建模仿真,可以在缺乏实验数据的情况下获得关键特性。微观层级模拟仿真的输出支持用于大尺度工程级仿真的输入,以此获取的电芯宏观性能结合实验测量数据进行拟合后,即可帮助研发人员快速判断不同使用环境中电芯宏观性能的优劣。结果表明性能。合作科研团队交付经验证的预测模型和工作流,供电芯设计工程师直接使用。
应用成果
- 开发预测电芯特性的工作流;根据实验数据进行验证和迭代
- 经验证的用于预测电芯输运性质特性的工作流
- 经验证的用于预测电芯内部电化学特性的工作流
- 经验证的用于预测电芯局部结构特性与力学特性的工作流
- 经验证的用于预测电芯热性能的工作流程
“与达索系统合作科研团队的紧密合作,使我们新产品的研发状况焕然一新。我们的工程师通过使用经验证的基于第一性原理3D化学建模与仿真工作流,创新速度加快了40%。“
— 汽车制造商电芯设计实验室(Cell Design Lab)经理
案例三:一家航空航天承包商借助虚拟实验降低项目风险
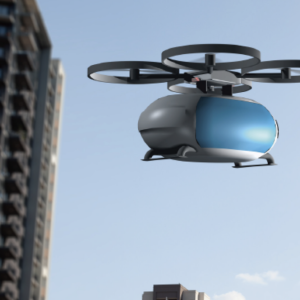
业务挑战
某厂商不同批次电池材料的不一致性导致所生产的电芯性能有剧烈的波动。
解决方案
合作科研团队对材料的微观结构进行建模,模拟关键的电化学机理。针对电极前驱体的虚拟孪生揭示了电芯性能不一致是由不同批次原材料制成的电芯微观结构和形貌的不一致所造成的。通过开展一系列基于“虚拟场景”的实验模拟不同批次原材料所引起的变化,并使用基于第一性原理3D化学进行仿真测试。合作科研团队提出在实际制作电芯前都应该预先进行主动的虚拟材料测试。并要求该厂商对每个批次的电池都开展这项测试。
应用成果
- 经验证的基于3D化学的模型
- 通过3D化学虚拟孪生获得深入的业务见解
- 开展一系列“假设场景”虚拟实验以模拟变化所产生的影响
- 理解厂商提供的电极前驱体材料不一致性导致电芯失效的根本原因
- 为厂商提供补救措施,以避免后续电芯性能的不一致
“电池技术中心(Battery Technology Center)借助合作科研团队的电池材料建模与仿真专业能力,为我们公司节省了大量的时间与经费。“
—航空航天承包商电池风控经理
案例四:个人设备制造商通过虚拟孪生降低故障率
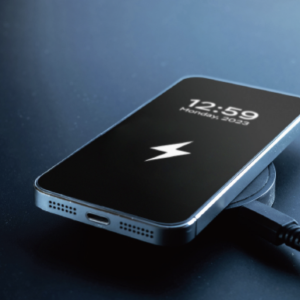
业务挑战
某特定设备制造流程导致高故障率,尽管对整个流程的其他“可调环节”进行了调试和优化,故障依旧存在。
解决方案
合作科研团队充分发挥其在材料和流程化学方面的专长,对故障的可能原因提出了三个假设。采用先进技术能力(ATC)对研究对象建模,并对每个假设进行了虚拟测试。通过创建原子尺度与介观尺度模型,来模拟制造流程的相应步骤。将虚拟测试的结果与观察到的行为进行比较,揭示故障难以根除的原因。当确认原因之后,采用适当的ATC制定该问题的修复方案。
应用成果
- 基于3D化学模型对三种假设进行建模
- 从3D化学虚拟孪生中获取深入的业务见解,揭示导致故障的意外原因
- 针对性地修改制造流程,以消除此故障
“我们公司掌握制造流程的‘know-how’已有数十年。合作科研团队提供了针对此关键流程的‘know-why’,从而帮助我们将故障率从9%锐降至1%。”
— 设备制造商高级研发副总裁
案例五:设备制造商利用机械学习预测电池循环寿命
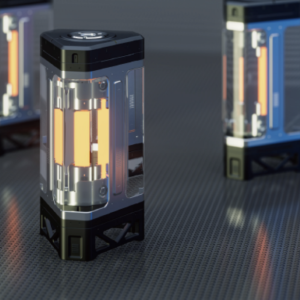
业务挑战
为了更好地满足消费者对产品质量的要求,厂商需要更可靠、更准确地预测电池使用寿命、循环寿命和工作温度范围。而这些数据的获取极为昂贵、耗时。
解决方案
在签署并严格遵守保密协议的前提下,客户提供关注的电芯内部数据用于合作科研项目。合作科研团队的专家根据提供的数据,以PipelinePilot为主要工具,辅以合作科研协作模式下特有的其他技术,训练并交付给客户独家专有的机器学习预测模型。
应用成果
- 机器学习模型从最初几次循环的数据预测出电池整体的循环寿命
- 创成式的模型设计可支持整合未来取得的新数据进行模型的迭代
- 为长时间周期实验提供更快速更经济的方法
- 便于非仿真专家用户使用的研发决策工具
“合作科研团队发挥自身在电芯领域的专业能力,再完美结合机器学习专业能力,为我们提供了高质量的电池寿命的预测模型”
— 设备制造商研发经理